来源:微矩电动
三合一系统的集成形式大体有两种,径向集成和轴向集成,最近刚好看到Vitesco在官网上发布了新一代三合一EMR4,里面介绍了很多驱动系统平台化定义方面的思考,我觉得很有意义,特意解读分享出来供大家参考。话不多说,我们先来看看Vitesco的这篇介绍。(“Vitesco Technologies” 为Continental集团前动力总成事业部)
可扩展的高效400V电驱动平台
1. 前言
随着电动汽车在市场上的显著加速,品牌、细分市场和车型的差异也在不断增加,最大限度地扩大电驱动系统适用性就显得及其重要。电驱动系统,如大批量生产的EMR3(第三代电驱动系统)和目前正在开发的EMR4,在系统级采用了多标准优化方法进行设计。与上一代相比,EMR4提高了高达5%的效率,显著提升了功率可扩展性,并大幅降低了成本。
提高效率和性能是整车对电驱动系统提出的技术路线和方向。为了促进EMR4性能提升,众多的影响电驱动效率和性能的链条已优化到细节。出于可扩展性的考虑,许多内部和外部接口也已标准化,以确保三个主要组件——电力电子逆变器、电机和减速器——可以按照需求定制的原则尽可能自由地组合。在电驱动系统的声学舒适性方面,重点是在整个工作MAP上对系统的噪声特性(噪声振动严酷度)进行了模拟、测试和优化。EMR4的开发从一开始就吸收了来自前几代电驱动系统的相关经验。
2. EMR4架构
为了更大的可扩展性,EMR4电驱动系统的基本结构与当前的EMR3相比已经发生了变化。所有三个基本组件(电力电子逆变器、电机、减速机)都在EMR4中直线排列(轴向集成);
有了这个基本架构,就有可能在不同的设计中连接两个最大需要变动性的组件,而减速器变速箱的修改要求可以在外壳尺寸内实现。这种内联安排形成了EMR4关键架构特性的基础。
在开发过程中计划的标准配置(对于A到J2段的车辆,即车辆重量级别从1800公斤到2800公斤)可以通过将电机长度按60毫米(入门级)、90毫米(基础级)或105毫米(增强级)三个尺寸来覆盖,如图2所示。根据设计,新开发的EMR4驱动系统提供80kW和最大230kW功率(10秒)。驱动系统的扭矩范围从1,700Nm到4,000Nm(10秒),可扩展性在模块的重量上也很明显。
根据驱动的功率需求,它的重量在45公斤到80公斤之间。根据之前的研究结果,与EMR3相比,EMR4驱动系统在WLTP中能够实现5.6%的效率优势,这将对车辆行驶里程产生明显的影响。
这些数值是通过对驱动系统中多个中心效应链进行系统优化得到的。这里通过许多详细的措施实现了改进的潜力。与优化后的EMR3相比,EMR4的效率提高了相当多,功率密度增加了20%以上,但成本进一步降低。尽管EMR4在许多地方都使用了高质量的材料,但材料的技术优势使得在其他领域节省了更多的成本,使成本得到优化。
2.1架构与电机
PSM电机的直径(其外壳直径)已经为集成EMR4固定设计。EMR4平台电机的定子外径为208mm,与EMR3电机相比,其直径略大于20mm。然而,电机性能提高的设计措施使EMR4电机的轴向长度比目前的轴向驱动器(90毫米而不是175毫米)减少了近一半。
定子现在每个沟槽至少有四层(而不是EMR3中的两层)。未来根据具体情况选择的层数(如4-8层)严格按照所需的成本要求和性能等级或电压确定。成本最小化和活动部件潜力的最大利用之间的平衡是要考虑的重要因素。
2.2架构与电力电子控制器
EMR4平台的逆变器是基于Vitesco Technologies (EPF4)的第四代高压电力电子产品。对于EMR4平台的功率范围,高度集成的EPF4逆变器可提供三个功率级别290A(“入门级”),550A(“基础级”)和820A(“增强级”)。Entry版本提供了一种经济有效的解决方案,输出高达80kW(10s)和扭矩1700Nm(10s)。基本版本适用于比较广泛的应用,功率输出高达135/165kW(10s)和扭矩2,500/3,000 Nm(10s)。增强型设计用于在2800Nm和4000Nm的输出,高达230kW的功率。
然而,在原则上,所有逆变器变体可以与每一个电机功率变体和每一个所需的减速器相结合。这需要满足与标准的大批量乘用车不同的特殊要求(例如,物流车)。逆变器尺寸只有270 × 221 × 126mm,是非常紧凑的设计。
2.3架构和减速器
根据电机的扭矩,平台包括三个版本的减速器,配置为< 2,000 Nm(“入门级”)、< 3,000 Nm(“基础级”)或< 4,000 Nm(“增强级”)。
预计i = 9.3和i = 11.64之间的减速比。与上一代相比,这一减速比已经扩大,使最佳利用电机的更高峰值速度成为可能。在减速器中,这一高减速比措施可以显著节省电机成本,在更高质量材料的成本方面提供了降成本机会。
减速机的设计高达16000 rpm的输入速度和255 Nm的电机扭矩输入。减速器提供高达3000牛米的轴扭矩的输出。
最大允许轴转速为1720转/分。电动驻车可以选择集成到减速器中。
3. 影响效率的因素优化
在世界范围内,进一步提高电动汽车效率的趋势是显而易见的。里程和电池尺寸/电池成本的考虑,以及旨在控制空气污染和减缓气候变化的法律要求都有助于这一点。此外,电动驱动效率的进一步提高也增加了汽车的吸引力,因为由此产生的系统成本降低了。WLTP中的Wh/km被用来衡量能源消耗。
众多的单体因素决定了一辆车的效率。虽然其中大部分都是整车造成的,但动力系统也有相当大的影响。
图3以集成驱动系统为例,说明了在整车上动力系统及其具体损失对效率的影响程度。一般来说,大约三分之一的损失是由驾驶造成的,大约三分之二是由整车造成的。
在电力电子逆变器、电机和减速器方面,EMR4取得了进一步的进步,提高了车辆的整体效率:与上一代相比,EMR4的效率要高得多,在WLTP工况中,平均每辆D级车的总能耗可降低5.6%。
3.1 电机和逆变器效率提升
在EMR4平台的Active parts中,使用了非常薄、高强度硅钢片制成的层压铁芯,以更少的材料使用实现更高的电机速度。现在最大速度是16000rpm (EMR3: 14000rpm),通过提高齿轮速比降低电机扭矩从而节省电机材料。另外,EMR4电机的持续功率方面也进行了大幅度改进。由于大大降低了损耗和优化了冷却结构,该电机可以在最高转速下持续输出40 - 80 kW。由于电机长度短,设计紧凑,散热也更有效,因为热量从电机中心的热点到其边缘散热有更短的散热路径。
增加的齿轮减速比(见2.3节)意味着在相同的轴扭矩下需要更低的电机扭矩。结合新的转子钣金切割和磁阻的增加,磁钢重量显著降低,功率保持不变,效率提高。
EPF4逆变器的工作电压为210 V至470 V, PWM开关频率为2至12 kHz。根据工作点的不同,磁场定向控制(FOC)算法分段应用,传统空间矢量脉宽调制(= SVPWM在低速时,以启用更高的电流)、同步PWM (= SynchPWM在中速范围)、不连续PWM (= GDPWM在中速范围)和磁通双向调制(= FBM在高速范围)。电机外壳前端的转子位置传感器提供转子位置信号。图4显示了在仿真过程中用于评估电机和逆变器损耗的参考操作点。比较高的效率增益,特别是在高速旋转时,正是因为更薄的电机硅钢片应用叠层数增加形成大量减少铁损的效果。
4. EMR4平台化实现方法
集成电驱动系统的应用范围日益扩大,只有在性能、效率、成本、尺寸和重量方面具有高度的可扩展性,才能满足市场的多样性要求。可扩展性最终意味着能够根据应用将相关主要组件组合在一起来满足需求。考虑到定义驱动系统所需性能特征的大量参数和它们之间复杂的相互作用,要彻底地落实到细节在设计方面是非常具有挑战性的。
例如,在EMR4平台的开发过程中,我们进行了广泛的灵敏度分析,以确定WLTP中单个参数对电驱动系统效率的影响,如图6所示。
为了实现预期性能特性和相关成本的最优权重,开发人员在这个多标准的开发阶段使用了专用工具iMCO,如图7[3]所示。
5. 内部和外部接口
前面已经提到,在设计集成驱动系统时,分离设计的电驱动的复杂性已经从整车角度已经完全简化了,复杂性转移到驱动系统内部。在这里,复杂程度的转移也可以从驱动系统内部和外部的众多接口中得到证明。图8显示了驱动系统内各个功能之间的内部接口,用灰色突出显示,绿色圆圈显示整车的外部接口。
为了实现预验证EMR4平台组件的全面扩展性,所有主要组件,即逆变器(三个版本),减速机(三个变种),转子和定子(每个三个长度)以及电机外壳(三个长度)和轴承板(两个版本的“盖”)都有关于内部和外部接口的明确定义。这使得使用统一的接口组合不同的组件设计成为可能。
结构噪声和电磁辐射在也是电驱动系统关键指标。为了最大限度地减少电动驱动中结构噪声对车身振动的影响,已经对所有运行情况下的驱动系统的声学质量(噪声、振动、严酷度、NVH)进行了大量的优化工作,如图9,10所示。在EMR4平台上,已经在A-sample基础上成功地进行了验证仿真结果的测试。
这种模拟技术还可以用于优化支架形状,避免导致车辆结构设计相关激励共振。
EMR4平台的电磁兼容性符合CISPR25-2016 Class 3标准,如图11所示。
6. 小结
EMR4平台的开发已经吸收了三代电驱动系统的产业化经验:截至2021年初,仅EMR3就已交付客户超过15万台。EMR4的效率和性能在降低成本的情况下得到了显著提高,甚至与已经进行了优化的EMR3驱动系统相比也是如此。特别是,新平台的高可扩展性使得EMR4驱动系统在各种不同车型中具有高性价比的使用前景。
EMR4平台目前的可扩展输出功率在80 kW至230 kW之间,质量仅在45 kg至80 kg之间,高功率密度支持大量车型向电气化过渡。为了涵盖高于或低于指定的当前范围的性能要求,将于2021年开始开发投资组合扩展。
通过系统的成本优化,EMR4平台帮助电动汽车的购买成本更接近以往内燃机汽车的标准。由于EMR4驱动系统的效率进一步提高,电池也降低了成本。
EMR4平台代表定制的现成解决方案,始终专注于产品的标准化和模块化。在系统限制下,客户特定的差异化是通过集成和系统专业知识形成的。这种方式创造了成本优化和个性化之间的平衡,辅之以多年的生产经验和质量控制。基于这一战略,Vitesco Technologies 正积极与客户和供应商合作,促进电动出行的增长。
平台化产品思考
三合一电驱动系统如何进行平台化相信很多公司都分析过,Vitesco EMR4的平台化思考给了我们很多启迪:
① 集成形式选择轴向集成,这样集成就把电机和逆变器进行了解耦,选择了外径比较大的电机,功率的扩展通过铁心叠厚进行调整,铁芯冲片就可以完全平台化;
②从逆变器电流规格上看,IGBT模块应该选的是HPD封装,通过不同芯片数量和散热底板组合形成了不同的电流规格;
③减速器选择了大减速比,可以减小电机扭矩,减小扭矩可以直接减少电机材料用量,降低电机成本;
基于电机效率,性能,成本等多标准优化提到了专用工具iMCO,这个也可以参考。
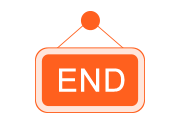